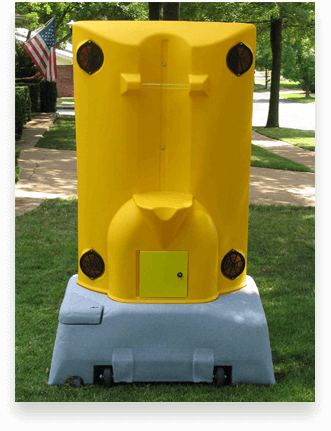
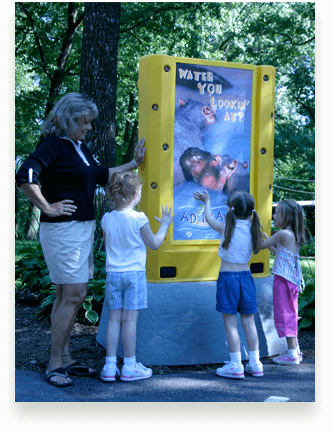
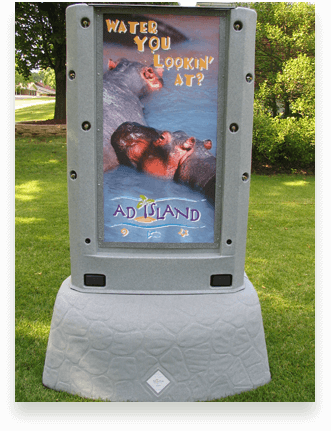
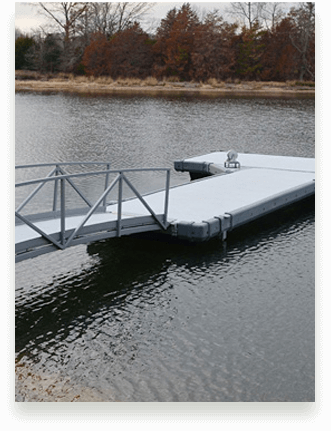
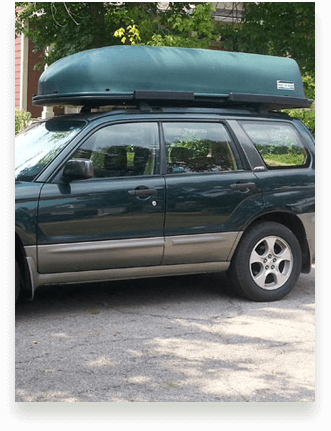
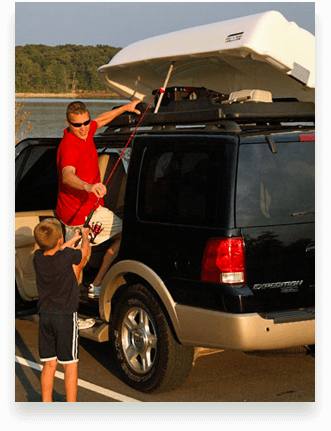
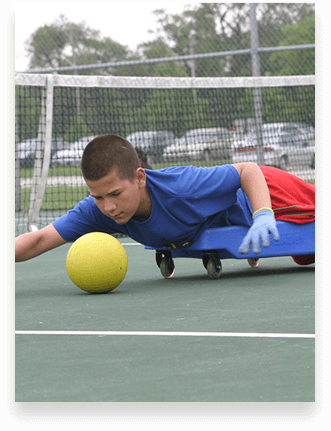
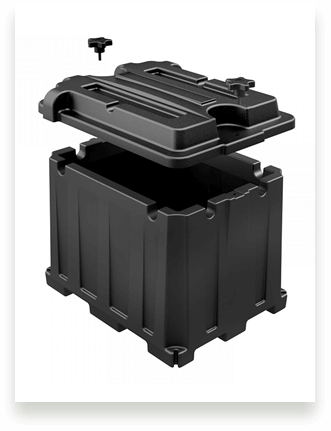
Rotational Molding Design Firm
I specialize in rotational molding design. As a freelance product design engineer, I can bring my 25+ years’ experience with molding design to your project. In addition to rotomolding design, I can provide consulting and FEA services to make sure your product will be a success. I can also help you source the right rotational molder based on the requirements of your project. I work across the US and Canada with most of the rotational molders and mold makers and can help steer you in the right direction.
I offer competitive rates and turnkey product design and development services. I am an expert level SolidWorks designer and can also provide 3D modeling services of mating components to your rotationally molded product.
Molding design services include:
- Rotational Molding Part Design & Consulting
- Solid Modeling & Design for Rotational Molding
- FEA Analysis
- 3D Scale Models
- Product Design & Development
- Project Management
- Tooling Design, Acquisition and Project Coordination with the Rotational Molder
If you’re looking for rotational molding design assistance, I’d be more than happy to discuss your project. I do not charge for initial consultations, just give me a call at 330-322-8707.
More About Rotational Molding Design
Rotational molding design is sort of a strange animal. Like other plastic design, you have to be aware of draft, undercuts and parting line location to name a few things. Unlike other plastic design, in rotational molding design you don’t always get exactly what you set out to accomplish. The reasons for this are varied. It ranges from what the individual molders are separately capable of to what the specific resin materials shrink rate does to the accumulation of tolerances in an assembly. Rotational molding design leans heavily on experience to create a proper part for this process. This isn’t to say that its rocket science and that not every designer can do it. It’s to say that depending on the complexity of the part and what it’s function is, you better have some familiarity with this particular process as well as be somewhat familiar with the molder that will be molding the part. Otherwise things can get ugly in a hurry.
We here at Blue-Reed, LLC have plenty of experience with rotational molding design. I myself, have 25 years of experience in the industry. Part of that was as an engineer for a large rotational mold maker and the rest as a product designer. This gives me a leg up on a lot of designers in that not only do I have plenty of experience in rotational molding design, but I have experience in rotational mold making engineering. Not only can I see what problems that may be had with molding, but I also know what can and can’t be done with the mold if there are molding problems. Knowing the types of molds available to the process and what will work for the part is an advantage. There are cast aluminum, sheet metal, and machined molds. Generally, you don’t want to use a machined mold for a part that is really large. That’s not to say that you can’t do it, but it can get very expensive. Machined molds can be used for parts that need a close tolerance and aren’t too large. Cast aluminum molds give you the most freedom so far as geometry goes. Sheet metal molds, generally speaking, are usually not as expensive and for parts where the geometry is not as complex. There are some sheet metal molds made by the better mold makers that you can’t tell by looking at the part whether the part came out of a cast mold or a sheet metal mold.
Knowing when to use what type of mold is crucial in rotational molding design.As mentioned before, using draft and being aware of undercuts is crucial to rotational molding design as well as any other plastic part design. In some parts, a pocket or recess is something that has to be in a particular place and can’t be moved. Knowing that it can be put there and formed with a loose mold piece and not be a concern to the mold maker nor the molder is a big piece of knowledge. On outside walls, draft can be minimized or taken out completely if the part will shrink away from the outside wall. If you have a deep core next to that outside wall, the molder may have trouble getting the part out of the mold. This is an area that may not shrink as much as you may want it or think it should. In rotational molding design, variable shrink can be considered in that a part may not shrink vertically, for example, as it will horizontally. This can be taken care of in the model or pattern stage before it goes to the foundry.
Threads are another peculiar thing in rotational molding design. A certain style of thread can be molded into the plastic. It’s a modified buttress thread. The size of the thread and where it is can be a problem if not designed into the part properly. Small threads are usually taken care of with metallic molded-in inserts. The location and spacing on the part of these inserts is a part of the design process that needs to be carefully considered. Shrink can affect their location and you need to be aware of everything mold wise that will determine if they can even be held in the mold or if there is enough room for the mold operator to put them in the mold.
These are all just parts of the whole that should be taken into consideration in rotational mold design. There are things I haven’t talked about such as mold-in graphics for logos or logos molded-in relief into the plastic. Through holes and how they are made and a whole host of other considerations the designer needs to take into account and share with the mold maker and molder as the design process is going. This means that although you may think you have an easy part and it’s an easy thing to design, you should probably have someone familiar with rotational molding design take a look at it to be sure you have a successful project! We here at Blue-Reed, LLC have the experience you need.