The Struggles of a Plastic Machining Manufacturer
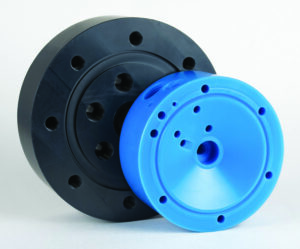
CNC manufacturing is a complex process. Customers and engineers expect complex parts delivered quickly, and at competitive prices. The whole package. Nevertheless, these things can only coexist in a perfect world. There is always the possibility that something will go wrong, or that a problem will be more complicated than expected. CNC manufacturing is a tough business that requires people with a competitive attitude for success.
Things become more complicated as you add variables like the type of material used. Different materials require different treatment methods. Hard materials require harder tooling, while softer materials can lead to the formation of galling or debris on the cutting surfaces. With different materials, there are many issues and considerations, and that’s just the tip of the iceberg.
Plastic has a different makeup and characteristics from metal, which means cutting it requires a different understanding. So what, exactly, are the differences?
The following are five challenges a plastic machining manufacturer might face when
cutting plastic.
Cracking
Chips and cracks are common with brittle plastics. Sharp corners and thin cross-sections are more prone to cracking and chipping. It is, therefore, necessary to machine these parts slowly. This can be achieved by choosing the right tool path and cutter. Select a cutter that is ideal for the material you’re cutting, or call a tool shop to get a recommendation. In order to avoid plastic cracking under heat, it is recommended to use coolants and fans.
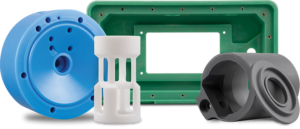
Burring
Most machining processes result in burrs, but they are particularly common when
machining plastics due to their softness. Many burrs can be removed by machining additional passes, but others must be deburred later by hand, which is usually the most effective way to catch any stragglers.
Warping
The parts are prone to warping when machining plastic sheet stock. The deformation of thin plastic sheets or certain types of plastic resins is more likely to occur. Changing the tool paths can reduce the effects of stress that causes warping. As with cracking, temperature control and feed speeds also have an impact on how the material behaves. With the experience of a plastic machining manufacturer, these problems can be circumvented.
Fixturing and Tooling Complications
Material/parts that are too soft or brittle can be difficult to hold. The parts can be damaged or warped if the fixture is over-tightened. Plastics wear out cutters more quickly, often drastically. A good cutter must be carefully selected, as well as monitored frequently. In plastics machining, uncoated tools produce a smoother finish, but they are more prone to wear and tear.
Distorted Raw Material
As a result of their malleability, plastic sheets and rods are not always perfectly flat. Consequently, feeding and fixing them can be challenging. It’s essential to qualify plastic raw materials prior to machining. Utilizing techniques such as fly-cutting,
a plastic machinist can resolve these issues.
Finding a Quality Plastic Machining Manufacturer
Entropy is an ever-present issue in the manufacturing industry. Every now and then, something goes wrong, but the experts are the ones who can fix it. For a plastic machining manufacturer, having an understanding of what could go wrong, and being prepared and equipped with the right tools to solve it, is half the battle.
To find the best plastic machining manufacturer, make sure you vet your options. The issues listed above are no joke, and it takes experienced machinists to be able to handle and plan for the stumbling blocks in the road to a good part. For Blue Reed’s pick in Ohio, we would suggest Jaco Plastics. They are an experienced and reputable plastic machining manufacturer in the North East Ohio region that is known to take on high volume orders, with a great eye for quality. Visit
Jaco today to see how they might be a good fit for your next project.
Keep Reading:
Molding vs. Machining