DESIGN GUIDELINES FOR
ROTATIONAL MOLDING
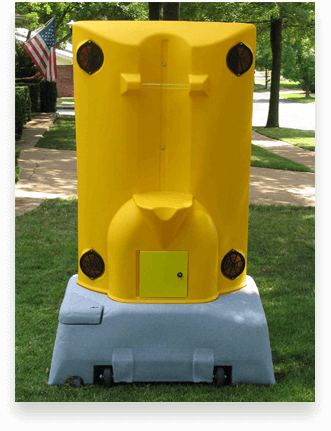
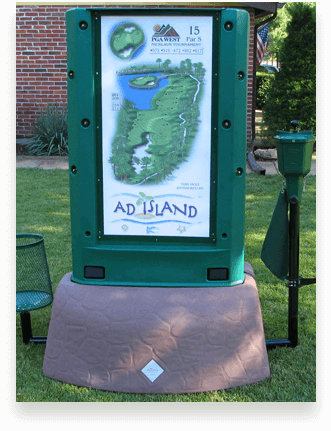
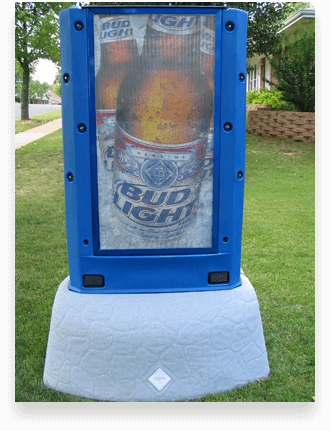
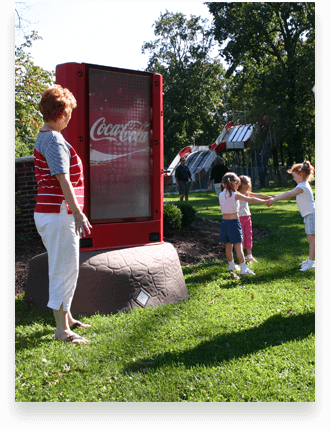
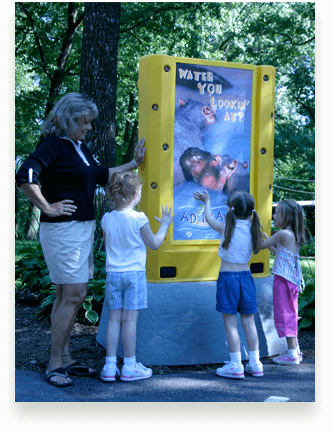
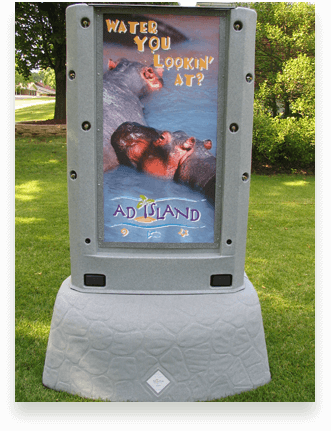
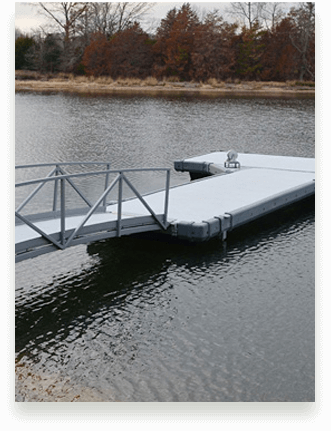
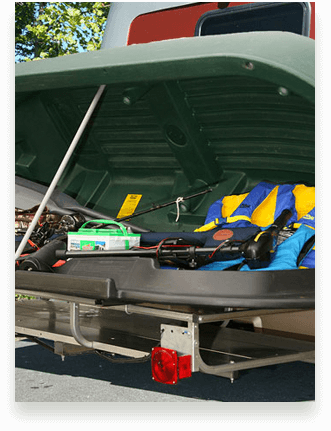
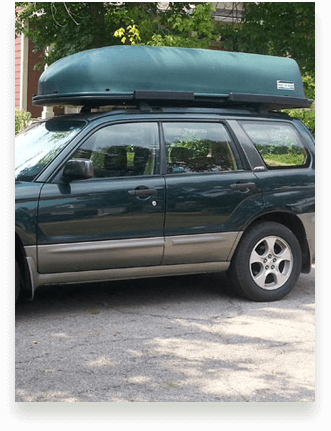
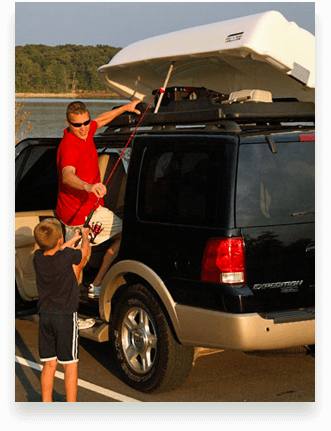
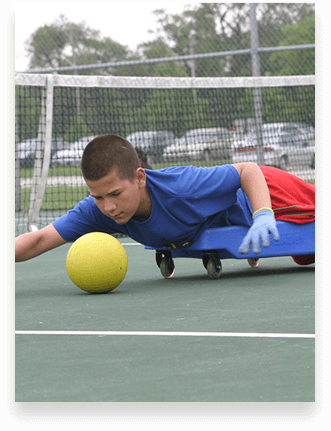
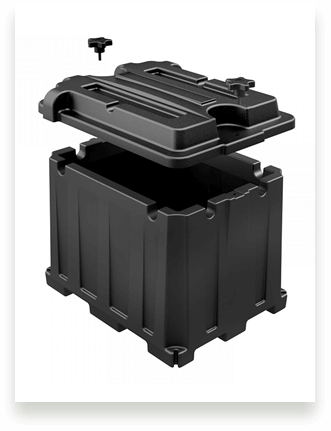
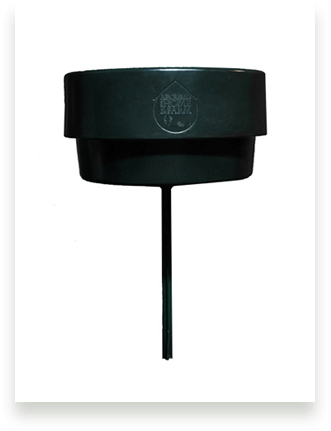
Parting Lines
When designing your product keep in mind how the mold will open and close around the product. The least expensive, least maintenance mold has two pieces. If your product will require multiple piece molds, you are increasing the chance of wear and flashing due to the operator handling and additional parting lines required. The toy industry has mastered the concept of 2-piece mold/product design, resulting in low cost tools used in high production. Two types of parting lines are predominantly used in cast molds; tongue and groove and flat with dowel pin register. Tongue and groove maintains better registration over the life of the mold. Flat and dowel may require maintenance as dowels loosen. A rule of thumb for dowel spacing on the parting line is every 6-7 inches. One of the biggest maintenance problems that molders experience is partline deterioration and flashing, the following steps will help in reducing this problem. Avoid parting line on sharp corners or along knife edges, always add a radius. Avoid vertical parting lines. Multiple piece molds should be designed whenever possible to use slide system or hinge system to guide opening and closing of multiple piece molds, this results in less damage to part line and ease of operator performance.
Inserts & Pull Pins
Today’s products require multiple piece molds, various types of inserts (stainless, alum., brass), molded threads for caps, internal threads, caster mounting plates are molded in product. Numerous designs of insert holders and pull pins are available depending upon the specific application.
Shrinkage
Various resins have different shrinkage, .007, .025, .030, .035 in/in. Cast aluminum molds also shrink .011 in/in. The molding process can also vary these shrinkages. Restricted areas will also vary the shrinkage to some degree. The type of mold release or permanent coating will have varying shrinkage. If you are trying to create a round, it is recommended that you part around the circumference not across the round since the parting line will restrict the material shrinkage and force the part into an oblong.
Flatness & Stiffening
Since Rotationally molded products are hollow, it is difficult to ensure flatness on a product. To counteract anticipated warpage, we may add a crown to the model or reinforcing ribs to the product. Process control is imperative. Reinforcing or stiffening ribs must be designed as a hollow element similar to corrugated sheet. Good proportions for a rib are a height of 4 times the wall thickness, and a width at least five times the wall thickness. The greater the height of the rib the greater the stiffness. A rectangular vs. rounded rib will provide better stiffening. The side walls of the ribs should have draft or be tapered to avoid the part hanging up on the rib. Kiss-off or two-closely spaced walls that mold together also provide additional strength. The kiss-off area should be 2 times the wall thickness plus .030 as a starting point, although this can vary. However kiss-off or (wall to wall support) may cause surface deformation, in many applications kiss-off or wall to wall support may not contact each other and still achieve the support needed.
Radiuses & Angles
Due to nature of how the material flows and forms, sharp corners usually result in blow holes and porosity in the corners. Adding a generous radius improves the molding of corners and distributes the stress over a broader area adding to the product’s strength. The minimum recommended angle at the corner of a part for polyethylene and PVC is 30°, nylon is 20°, polycarbonate is 45°. Corner angles less than these amounts can result in a bridging of plastic, increased porosity and excessive shrinkage.
Draft Angles
Incorporating draft angles perpendicular to the parting line, will reduce warpage when demolding a product in areas where the product shrinks against/around the mold. For example, if you are molding a donut shape. The outer diameter will shrink in free of the mold wall. The inner diameter will shrink against the mold requiring draft angles here.