DESIGN GUIDELINES FOR
ROTATIONAL MOLDING
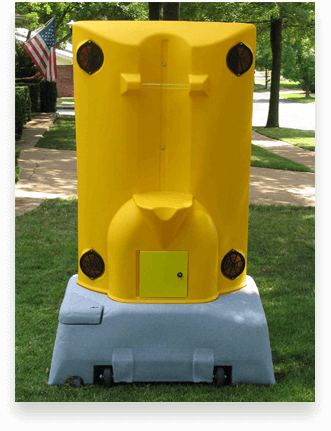
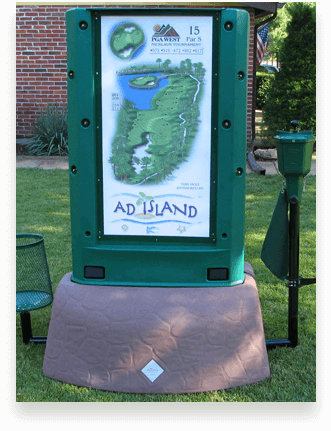
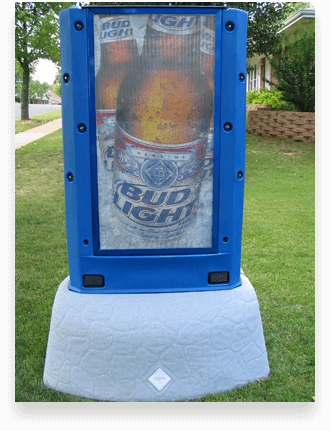
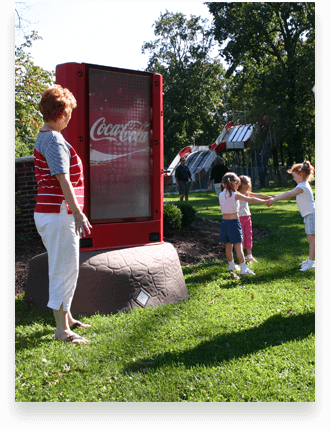
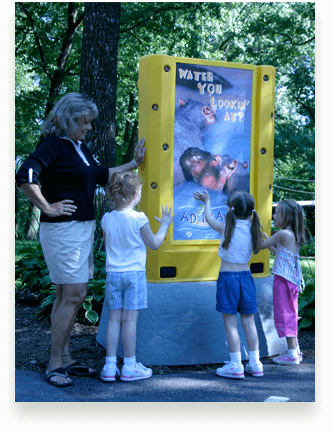
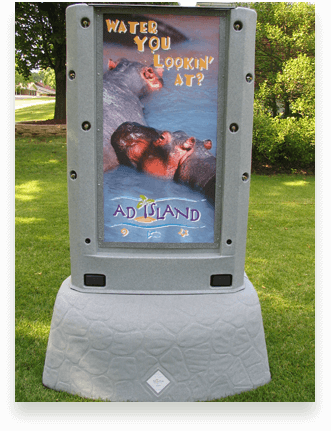
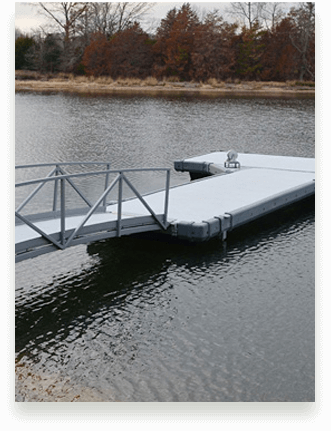
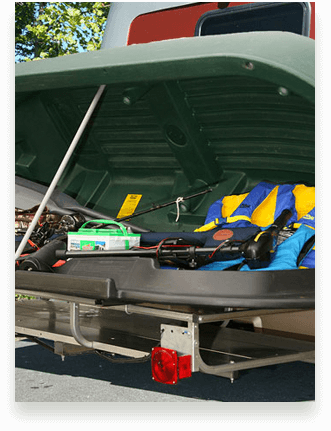
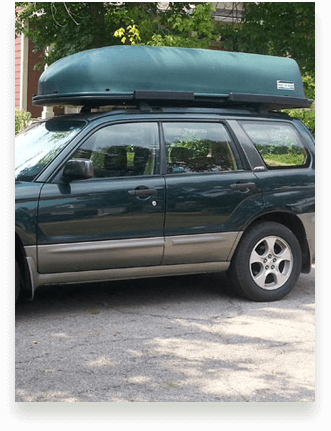
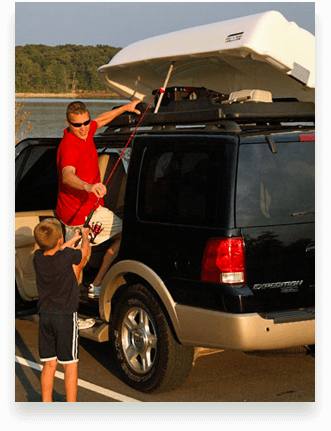
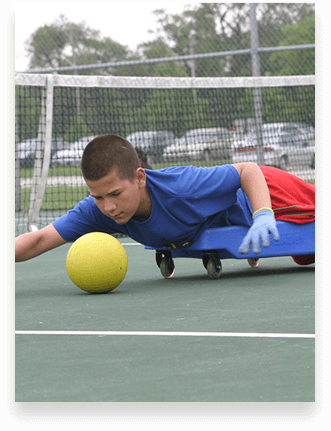
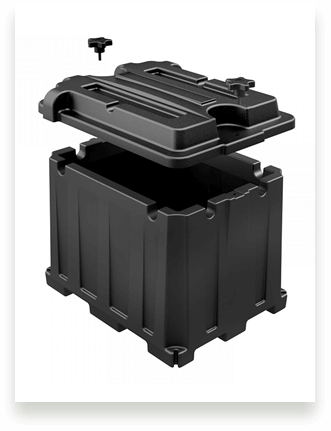
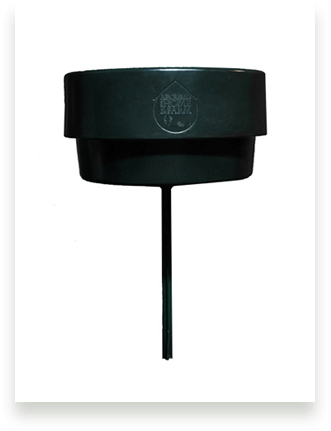
Venting
Due to gasses that are expelled when the resin cures, a vent hole is required in all molds and therefore products. The size of the vent is dependent upon the volume of the cavity. Formula to determine vent size is 1/2″ i.d.. vent for every cubic yard of volume. Multiple vent holes may be required for larger, more complex parts.
Double Wall Products
For material to flow and form properly, it is recommended that the distance between the parallel walls be a minimum of five times the nominal wall thickness of the part
Wall Thickness
Uniform wall thickness products is one of the inherent benefits of the Rotational molding process if all areas of the mold achieve uniform heating. Basically the hotter the inside surface of the mold gets the more material will form in that area. Therefore shielded areas and deep cores will reduce the amount of heat that are gets resulting in thinner walls in those areas. Steps must be incorporated in the mold design to ensure even wall thickness. Through the use of air amplifiers, preheating molds, black paint, heat fins and pins, and protherm, the molder can actually control the product wall thickness to achieve different wall thickness as required by a specific product design.
Loading
Material is usually loaded into the mold cavity when the mold is open. If there is not enough room to load material with the mold open, a fill port can be added. The fill port enables the operator to load the mold when closed. If there is still not enough room for material, a drop box can be added to provide a second or additional charge of material during the cycle.
Drop Boxes
Are primarily used to mold multiple layers of material to provide insulation, strength, multiple colors, foaming, and/or differing internal/external part requirements. The drop box usually mounts on the outside of the mold and holds a second charge of material. After the first charge inside the mold cavity has formed, an air actuated cylinder inside the drop box releases the second charge into the mold. A second drop box can be added to produce products with 3 layers of material such as PE skin – foam – PE skin.